Sintered NdFeB Material Grades
A brief overview of properties, nomenclature, and selection.
When selecting a permanent magnet material several properties must be considered. Residual induction (Br) and Coercivity (Hc) will typically be the most important. Induction (B) is what does the “work” in a permanent magnet. It is the flux emanating from the pole face. Coercivity (H) is, simplified, the resistance to demagnetization. Permanent magnets operate on a curve with these two properties on the axes (B on the Y-axis, Br being the point of intersection, and H on the X-axis, Hc being the point of intersection). Where they sit on this curve (how much average flux density they induce or how close they are to demagnetization) is a function of the shape and circuit of the magnet. The curve is unique for each material grade.
In selection, one must balance the expected output of the magnet with the risk of demagnetization. Typically, one trades a higher coercivity for induction (rare and expensive elements, heavy rare-earths such as dysprosium and terbium replace some of the neodymium in these higher coercivity materials, causing lower induction, but more protection from being thin, opposing fields or temperature).
In material grade nomenclature, for example, N48SH, the N stands for Neodymium, indicating the material is a sintered Nd2Fe14B permanent magnet. The numerical property is not straight-forward. It is the MGOe value of the magnet (Mega Gauss Oersteds, a unit). This is an amalgamation of the two properties which we typically consider. It is the max energy product of the magnet, the point on the curve where the induction and coercivity are maximized (the largest rectangular area able to be made under the curve). At that max energy point, the induction and coercivity can be multiplied to get the max energy product. Only in rare circumstances is the magnet operating at this point. In general, the takeaway is that the higher this number, the more flux the magnet channels (stronger), even though it is an indirect measurement. Because this is not the direct induction property, a value twice as high (comparing N28 to N56), does not mean a magnet is twice as strong, or is producing twice the flux. The increase, at the most favorable shape, would be in the range of 30%. Similarly, the holding force difference between an N50 and an N52 magnet, shape dependent, will generally be 1-3%. Finally, the follow-up letters detail the coercivity level. The higher the coercivity, the harder it is to demagnetize the magnet (permanent loss of flux potential). Magnets demagnetize from a number of factors including shape (mostly thickness), temperature, and opposing fields. Increased coercivity lowers induction and increases price, but the material grade selection is determined by the shape and environment of the magnet. Calculations and simulations must be done to determine the correct coercivity for a given design or system.
Following is a table of available NdFeB materials by max-energy-product and coercivity. Lower on the table will induce more flux in the circuit, further right will be more resistant to demagnetization. Since the added elements for higher coercivity partially displace neodymium, they typically lower the possible induction of the magnet, creating a challenge when producing magnets with both a high induction and high coercivity, leaving the bottom right-hand corner of the table empty. Many technological leaps forward (such as GBD, grain boundary diffusion, or permeating the outer shell of a material with a higher coercivity element) have allowed, very recently, the production of some of the highest MGOe magnets with M and H coercivities.
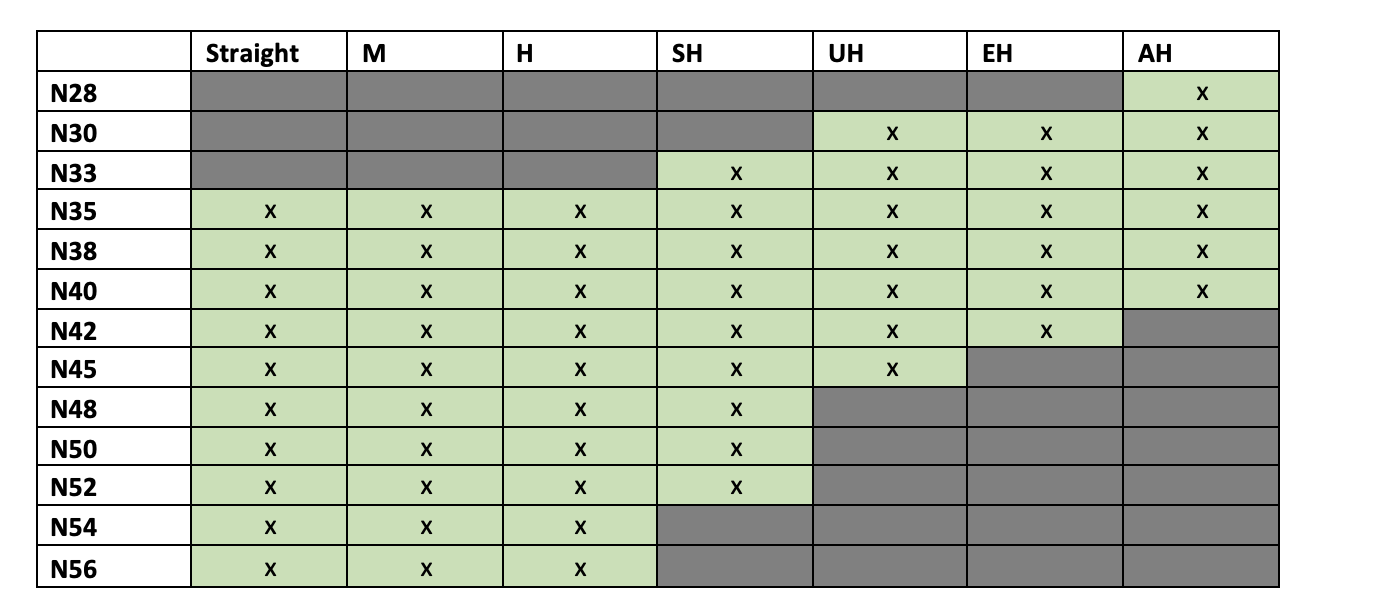
Table 1 – Available sintered NdFeB material grades.
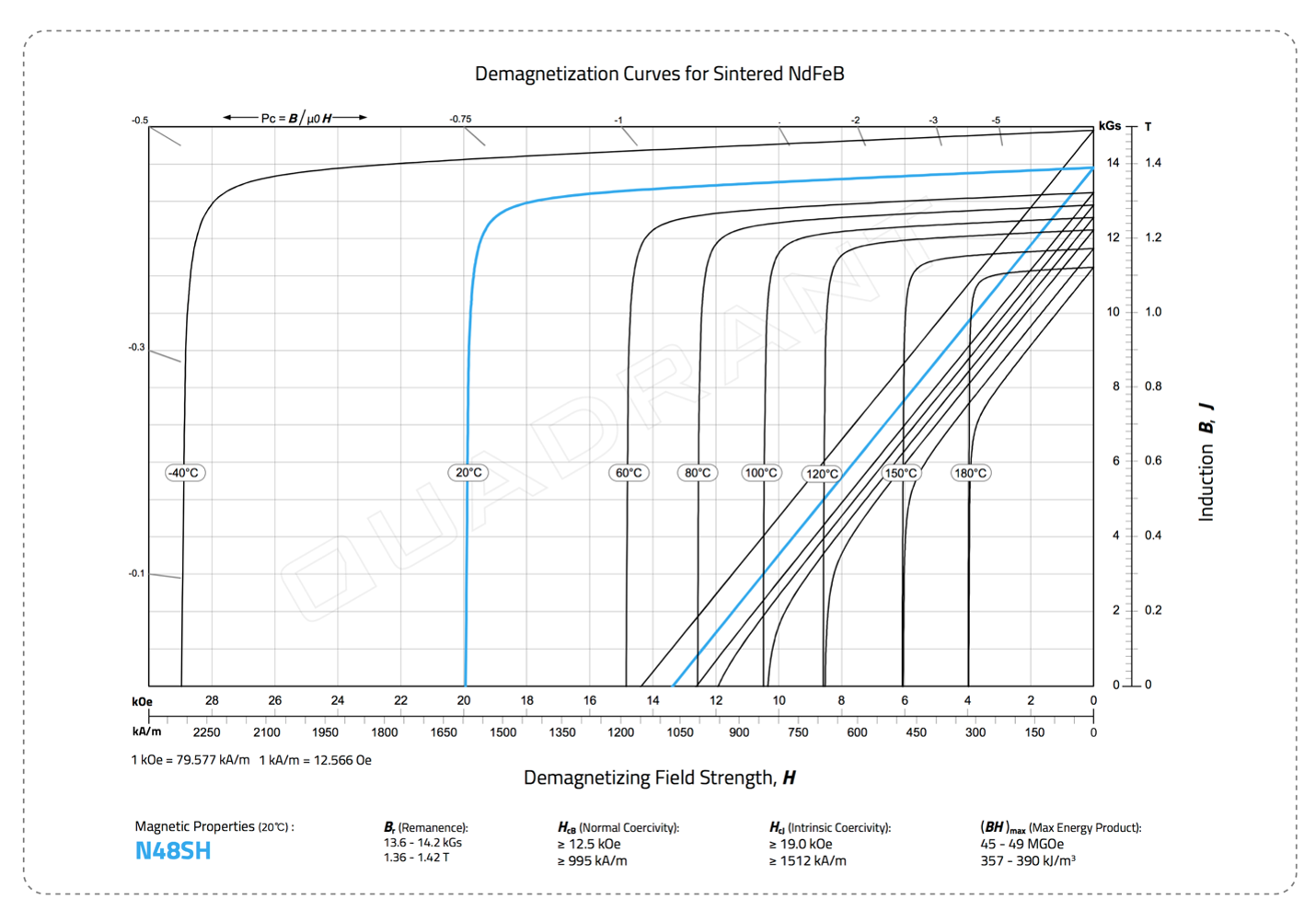
Image 1 – Example 2nd quadrant N48SH grade material hysteresis curve (BH curve).