Ferromagnetic “Soft” Material Properties and Selection
A discussion of description, function, and selection process of soft magnets in DC magnetic circuits
There is little difference between a permanent magnet and any magnetic target material or supporting material. They both have the same important quantities, with few distinctions. A permanent magnet (called a “Hard” magnet) is a ferromagnetic material that induces a magnetic field around it without any external influence. Typically, we just call this a magnet, but in actuality, by the broadest definition, anything is a magnet because every material falls into one of five categories of magnetism (although most of those categories are so weakly magnetic, we tend to ignore the effects).
The best magnets are in the category of ferromagnetic materials. We can break ferromagnetic materials into two categories, hard and soft magnets. Hard magnets (permanent magnets) are things like sintered NdFeB (neo magnets) and soft magnets are supporting materials like steel. There are two important distinctions between these two categories, without a firm line of where they fall, the line is so blurry that an unmagnetized hard magnet is a very poor soft magnet, and a soft magnet is a very poor hard magnet, but they do both still qualify in both categories. The most important distinction is coercivity and the other is permeability. Soft magnets have low coercivity (resistance to demagnetization), so they tend to demagnetize when external fields are removed (hence being magnets, but not permanent magnets). Soft magnets also typically have high relative (to vacuum space) permeabilities; while not required, I’ve listed it as part of the distinction because it’s a pretty poor soft magnet if the relative permeability is near 1.
Materials with a high permeability conduct flux well. Think of flux in a magnetic circuit like current in an electric circuit. Permeability would then be analogous to the conductivity of the material. The higher the permeability the more flux is induced in the material when an external field is exerted on it. Permeability helps to a point (saturation) where the soft material cannot carry any more flux (the relative permeability is a curve and it will eventually go to 1 when the soft material is saturated). Permeability and saturation induction are the two properties that are most important when selecting a soft magnetic material for a magnetic circuit.
Coercivity is a magnetic material’s resistance to demagnetization. It helps the material remain magnetized in the presence of opposing fields, increased temperature, or disadvantageous shape (a magnet’s shape alone can demagnetize it). Soft magnets typically have a low coercivity, so they are very easy to demagnetize. They will typically not induce any more flux after an external field is removed. When you put a permanent magnet near steel and then remove the permanent magnet, you will notice that in most cases the steel will go back to a demagnetized state; it is only carrying the flux from the permanent magnet (and it’s doing that really well!) but when the magnet is gone it’s just metal again. When the magnet is near, the steel becomes a magnet. Back to our electrical analogy, it becomes part of the magnetic circuit with the magnet as a battery and the steel as the conductor. Soft materials use this conductive ability to direct the field allowing us to design interesting magnetic circuits. I did write that shape does have an effect on what coercivity is required to demagnetize a material. Notice that if you put a magnet near an unraveled paperclip, staple, or nail, it can remain weakly magnetic and pick up other objects even after being removed from the permanent magnet. Long shapes need less coercivity to stay magnetized. This is how you build a very poor hard magnet out of soft material, as previously noted.
Below are two magnetic hysteresis loops. The first shows a soft material and the second a hard (permanent magnet) material as they are subjected to different strengths of an external field (H). As the H field gets larger, the flux density inside the material increases. Notice at high values of H, it stops increasing (in the first quadrant where H and B are positive), this is our saturation point. As the field is removed the material has less induced flux density (B). The thinner this loop, the easier the material is to demagnetize (coercivity, in this case Hcb or normal coercive force, is where the loop crosses the X-axis in the second quadrant). Why at 0 field both the hard and soft magnets still have positive B values (where they cross the Y-axis), when you would expect the soft material to have zero flux density when the external field is removed is outside the scope of this article, but as a quick note the shape of the object creates an internal H field (self-demagnetizing field) that causes it to sit in the second quadrant when there is zero external field. That’s why magnets with better shapes don’t demagnetize as easily; they have lower internal H fields.
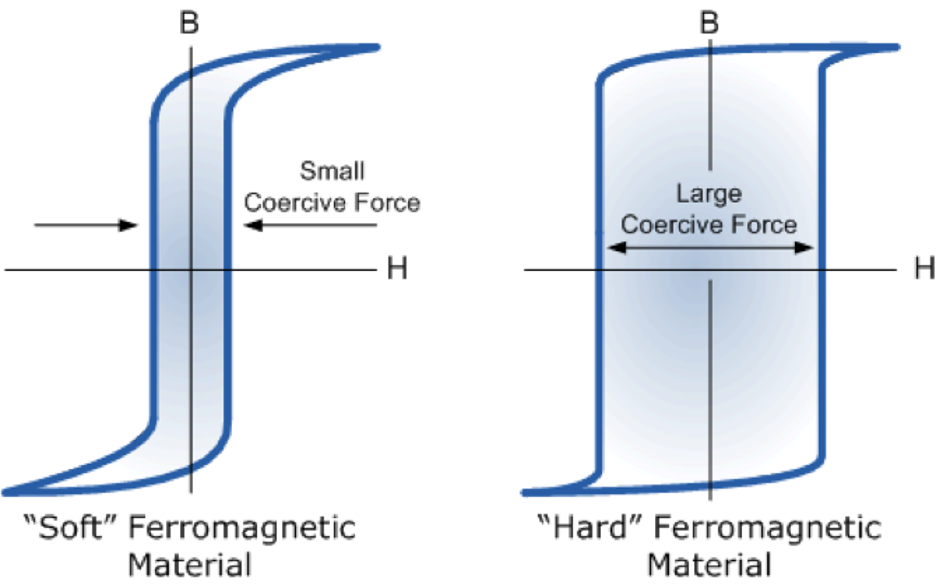
Figure 1 – The taller the B-H loop of the soft material, the higher it’s potential flux density (stronger holding force close up). The thinner the loop, the easier it is to demagnetize.
If we are considering holding force from a permanent magnet to a soft magnetic target, permeability is important at a distance. At a large distance the magnet has a small field, and a high permeability material will induce a large field inside from a small field (your target can be thinner and achieve the same holding force). This is also important for a magnetic shield in a small field. It will redirect more of the flux away from what you are shielding with a thinner shield, if the field strength from the source is sufficiently small. This makes mu-metal (a nickel alloy) a great shield from weak magnetic fields. However, if your permanent magnet is strong and close (the field around it is large, on the order of 0.5 Tesla), permeability will be much less important, and the saturation point will be the most important property.
Saturation induction is important in larger magnetic fields, as the field is probably large enough to saturate the area of the target facing the magnet. If you recall, this means the relative permeability has gone to 1 because we are so far into the first quadrant of the B-H loop. Permeability likely has little affect in this situation. For larger fields (typically over 0.5T, but this is a broad generalization as some materials saturate at VERY little field), a higher saturation material will allow the target to be smaller (if it can carry 1 Tesla across its cross-sectional area vs. 2 Tesla across its cross-sectional area, that area only has to be half as big to carry just as much flux) and still have the same holding force or effect on the circuit. It is also important for a shield. When the field is large, a small high saturation shield will deflect just as much field away from the shielded object as a larger low saturation shield. Basically, in large field situations, the higher the flux density, the thinner the soft magnet can be and in many applications saving thickness is the highest priority (consumer electronics).
You can also use soft materials to steer the field from a permanent magnet into a sensor or coil if that’s where you require it. This is a concept used heavily in VR (Variable Reluctance) sensors (used frequently as ABS sensors for anti-lock brakes or many gear sensors). You will choose your soft material again by its field strength requirements for the application. Sometimes a high permeability material is the answer, other times high saturation is required. There will also be other qualifications, like corrosion, where a 400 series stainless steel (while being thicker or having less holding force) will be advantageous of 1010 steel, because it withstands oxidation so much better. Many factors must be weighed with material selection (as is the case an any material engineering case).
I have only mentioned DC magnetic circuits with static fields being produced from a stationary permanent magnet, as this covers most of the properties and specifications for soft magnets. However, if magnets are moving or this is an AC (the fields are changing with a frequency or oscillating) magnetic circuit there will be other considerations. Permeability will likely become more important as the fields are changing so we want the induced field to dramatically change with a small field change to maximize efficiency in a lot of applications. I also mentioned permeability was a curve, but it gets far more complex at high frequencies. Electrical conductivity can then be important as the soft magnet will have eddy currents induced inside it from the changing fields (a moving magnetic field creates an electric potential in any conductive material) that can cause energy loss, heat, stray currents, and opposing magnetic fields (Lenz’s law, can be used in application as an eddy current brake). Also, the whole area inside the B-H loop may become important because the larger that area is, the more energy it takes to move from the first quadrant to the third (in application this can be used as a hysteresis brake. Notice there’s a lot about brakes; it’s because these two concepts discuss magnetic losses and you purposefully maximize those losses to heat something or slow a moving system down. They use these brakes on roller coasters quite often. They are unwanted side effects in most AC systems that need to be managed for efficiency).
Common Soft Magnetic Materials
Low carbon (1010) steel is a great magnetic conductor. Relatively high permeability (anywhere from a 100 to 5,000+ depending on composition (soft pure iron can in the 20,000 range) and large saturation induction (1.8 to 2T). It is inexpensive, but oxidizes easily, so requires a coating (typically electroplated nickel or zinc). As with most soft materials, it must be annealed (heat treated) properly for best magnetic properties. Cold working will change the magnetic properties and create stresses (and phase changes) that can greatly affect all the magnetic properties, heat treatment repairs some of this damage. This is typical for soft magnetic materials. It can be MIM’d (Metal Injection Molded) into many complex shapes. It is the go-to choice for shunts (magnet backings) to strengthen the magnet both magnetically and mechanically.
Iron-Cobalt (FeCo) is magnetically the strongest of the soft materials. It has the highest saturation induction (in the range of 2.3T) so it can carry the most flux per unit area. If a holding force target must be very small, this is likely your material of choice. It also corrodes (having a 50% iron content it oxidizes very easily) and must be coated, electroplated nickel and zinc are common. The permeability is not much different than 1010 steel (500 to 20,000 depending on chemistry and processing). It is more expensive than steel because of the cobalt content. Cobalt is also a conflict mineral that might weigh on your choice to use it. There are growing options for recycled cobalt from the best magnet suppliers focusing on environment and ethical responsibilities. It can be MIM’d into many complex shapes, but I’ve only see one supplier consistently do that and retain the high properties of the base material.
Stainless Steel 400 series / 17-4 will likely have a holding force that is less than steel or FeCo (it will either have a reduced force or need to be thicker to get the same force). This material really excels in harsh environments. It does not easily oxidize; therefore, it does not need to be coated and you don’t have to worry about the coating cracking or being scratched (and then rust forming) like you would most other iron-based chemistries. The saturation induction is up to 1.5T. The relative permeability is slightly less than steel (500-2000+ range).
As a note: 300 series stainless. This is typically non-magnetic (paramagnetic, relative permeability very near 1). It is often used to hold magnets together or to be used as a spacer or casing that won’t affect the field. If it is cold worked, it needs to be heat-treated or parts can become magnetic and effect the system. The same is true for aluminum, titanium, and brass that are often used around magnets as non-magnetic. All of these are electrically conductive, so consider eddy currents in changing fields.
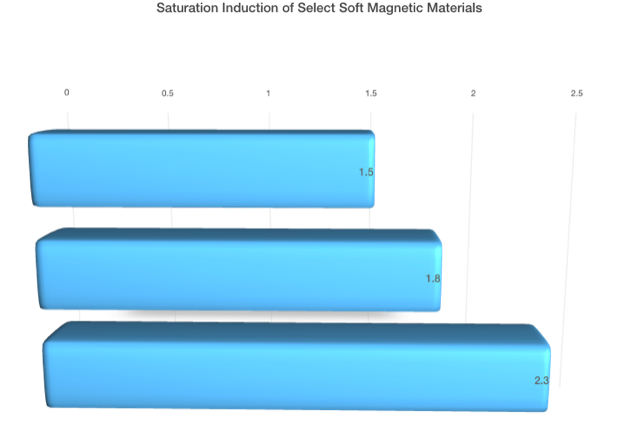
Figure 2 – Saturation induction comparison between 400 series stainless/1010 steel/ FeCo
Soft Material Manufacturing
It is usually possible to create soft magnetic materials in a variety of ways and shapes. Many more options are available for soft magnets than hard magnets. Most soft magnetic materials follow the same rules as typically metalworking. To name a few:
- Abrasive slicing and grinding
- CNC or milling options
- Stamping
- Metal Injection Molding